We look forward to transforming your Business
GC Lean Operations (PTY) LTD is a specialized consultancy dedicated to helping organizations achieve operational excellence through simplified lean operations. We understand that if you make things simple, there is a much greater chance of people understanding and implementing the ideas. To simplify Lean operations, as a team we specialize in Time & Motion studies, which is an important observed productivity time measurement, as it gives you baseline metrics and data points for your business. In addition, this process helps you learn more about the operational efficiency of your organization using clear time standards. From the time & motion studies we then partner with businesses to streamline processes, reduce waste, and improve productivity, ultimately enhancing profitability and customer satisfaction.
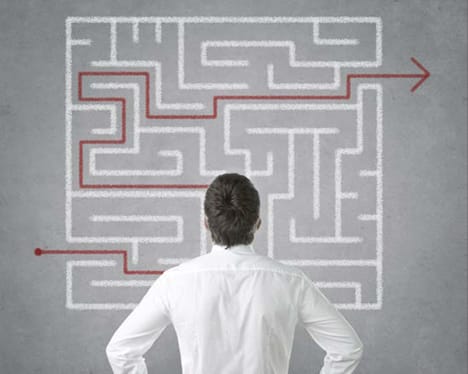
About Us
Our Mission
To empower organizations with the tools, strategies, and insights to drive continuous improvement, reduce inefficiencies, and create sustainable value through simplified lean principles and innovative solutions.
Our Vision
To be the trusted partner for manufacturers worldwide, setting the standard for operational excellence through simplified lean manufacturing practices.
Work done
Transnet Port Terminals, Durban (2022):
- Problem – logistic challenges at the Durban port hampering the exchange of goods. Demand not met due to poor operational efficiencies.
- Hypothesis – Delays are due to overhead cranes performing at a baseline of 6 lifts per hour, far below the target of 18 lifts per hour.
- Objective (s) – Increase crane lift efficiency to meet demand.
- Actions - Conducted detailed time studies to establish a baseline and identify factors contributing to low crane lift efficiency.
- Analysis: shift changes, tea breaks, unreliable cranes, shortage of trucks, manpower, pairing…
- Collaboration: Head of Maintenance, Millwrights, HR, Production Supervisors, Supply Chain & Procurement (availability of spares).
- Results – After 9 months, efforts led to an improved baseline from 6 to 16 lifts per hour per crane.
- Financial benefits – Lift on/lift off: R1495. Revenue increase per hour ~ R15k..
Rheinmetall-Denel-Munition (2023):
- Problem – Increased Market demand.
- Objective (s) – To increase the phosphate process throughput by eliminating manufacturing waste, reducing equipment downtime, and optimizing the use of available infrastructure and labor resources.
- Actions
- Mapped the current state of the phosphate process at the paint-shop.
- Conducted Time and Motion Studies.
- Identified all potential sources of waste in the process.
- Established the root causes of delays and inefficiencies.
- Proposed solutions and verified the effectiveness.
- Results – After 6 months, by addressing the root causes of delays and implementing these targeted improvements, the throughput of 155-mm artillery shells was successfully increased from 400 to 600 shells per 8-hour shift, achieving a 50% increase in production capacity.
Company XXX (2024):
- Problem –High fixed costs particularly related to labor expenses, which impact the overall operational efficiency.
- Hypothesis – Unreliable machinery, extended tea breaks, change overs, Operator skills and utilization.
- Objective (s) – To reduce labor costs by 10% while improving throughput by streamlining operator tasks, enhancing machinery reliability, and improving time management.
- Actions
- Applied Yamazumi charts to map out the production process, identified areas of wasted time, inefficiencies, and tasks that could be combined or eliminated.
- Conducted time and motion studies to analyze Operator performance, quantified downtime, and uncovered opportunities for optimizing tasks and processes.
- Evaluated the Operator count and workload distribution, leading to a reduction in the number of Operators by combining tasks while maintaining production efficiency.
- Implemented training programs to improve Operator skill levels, reducing delays caused by human error and improving overall efficiency.
- Collaborated with the Maintenance Team to address machinery reliability issues, HR to create training programs, and Production Supervisors to streamline workflows and optimize break times.
- Results – In 4 months, by streamlining tasks, addressing machinery downtime, optimizing break schedules, and improving Operator skills; this led to a 14% deduction in FTE Cost while still maintaining improved production levels.
- Financial benefit –FTE (confidential)
Company YYY (2025-Current):
- Problem – Reheat Furnace extracting slabs below the design capacity of 420 tons per hour leading to production backlogs, (supply < demand).
- Hypothesis – Reduced extraction capacity is due to the current extraction time of 176-sec per slab (400t/h).
- Objective (s) – Frist prize was to reduce extraction to 170-sec as per design.
- Actions - Conducted detailed time studies to establish a baseline and identify factors contributing to the increased extraction time.
- Results - After 2 weeks. We were able to extract a slab every 144-sec (500t/h), down from 176-sec (400t/h). This was achieved by the following action;
- The walking beam cycle time was reduced from 76-sec to 60-sec by fixing the valves, and increasing the speed of the hydraulic cylinders.
- The slab extraction time for rolling was reduced from 34-sec to 28-sec.
- The furnace door opening was triggered to open 10-sec before slabs is ready.
- Financial benefit – Steel prices @ R17 000/ton. Revenue increase per hour ~ 1,7M.
- Problem – High fixed costs mainly related to labor expenses, which impact the overall operational efficiency.
- Hypothesis – Operator Utilization.
- Objective (s) – To reduce labor costs by 10% while improving throughput by streamlining operator tasks.
- Actions – Yamazumi Line Balance Chart was utilized to balance workloads across Operators. From that we were able to combine activities effectively, and consolidate positions while ensuring that each operator's time was optimized.
- Results – In 1 month, by streamlining tasks, reducing waste, and improving Operator skills; this led to the combining of 8 positions into 4.
- Financial benefit – FTE (confidential).
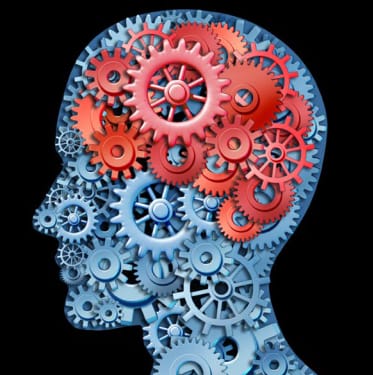
Our Values
- Safety First
- Customer-Centricity
- Continuous Improvement
- Innovation and Agility
- Sustainability and Responsibilityy
Core Services
Lean Transformation: A Lean way of implementing lean operational strategies to eliminate waste and optimize workflows by conducting Time & Motion studies.
Our People
Nimrod Ndlovu
BTech Industrial Engineering VUTNimrod Ndlovu is an Industrial Engineer with 3 years of experience in manufacturing and logistics. He began his career at Transnet Port Terminals, where he applied his skills to improve operational efficiency. He led a project that increased crane performance from 6 to 16 lifts per hour by conducting time studies and optimizing processes. Additionally, he implemented a 5S methodology within the maintenance team, reducing tool-search time and improving productivity. Nimrod then joined Rheinmetall Denel Munition as a Process Engineering Intern, where he helped achieve a 50% increase in throughput for phosphated shells by eliminating waste movements and optimizing processes through line balancing. He also contributed to restructuring the warehouse layout and introduced 5S to improve stock organization, reducing unnecessary movements and overtime. Currently, Nimrod is a Director of GC Lean Operations (PTY) LTD and a Consultant at ArcelorMittal South Africa which is fighting for survival. With the biggest challenge in his career he continues to focus on improving plant efficiencies to turn around the business which plays a critical part in the South African economy.
Phalalani Gule
MEng Industrial Engineering Wits | BEng (hons) Metallurgical Engineering UP | BEng Metallurgical Engineering UP | Supplier Genba Leader TSAMPhalalani Gule is a Metallurgical Engineer with 16 years of experience in the Steel Industry, specifically in Quality Management, Product & Process Development, and Business Improvement. He started his career as a Research Assistance at the Industrial Mineral and Research Institute (IMMRI) at the University of Pretoria where he gained valuable experience in Metallurgical Consulting. Working in Academia laid the foundation to focus, to structure, to write and to evaluate the arguments of others and to use them along with evidence to come to a balanced conclusion. After 3 years of service at IMMRI, Phalalani then joined ArcelorMittal South Africa as a Metallurgical Engineer and moved up the ranks to a Senior Engineer, and then a Quality Engineering & Control Manager for the Steel Making process, Plate & Hot Strip process. His most recent project was on Windtowers where the project included the development of APQP4Wind, PPAP, FMEA, Control Plan, Lean, 5S, Quality, and Project Planning & delivery. Phalalani is currently a founding member and a Director of GC Lean Operations (PTY) LTD and working with Industrial Engineers in implementing Lean manufacturing principles at AMSA.
Why Choose Us?
Expertise
A team of experienced lean practitioners with extensive manufacturing knowledge. We understand that if you make things simple, there is a much greater chance of people understanding and implementing the ideas.
Time & Motion studies
These are systematic methods used to analyze the efficiency of work processes and improve productivity by studying how tasks are performed. We believe that while certain techniques from lean operations can help reduce waste in organizations, but without clear baseline metrics or data we run the risk of missing areas of inefficiency.
Proven Results
A track record of measurable improvements in productivity, cost reduction, and lead times.
Industries Served
Manufacturing
Optimizing assembly line processes to reduce production time.
Logistics
Streamlining warehouse picking and packing workflows.
Healthcare
Improving patient care delivery by analyzing the movement of nurses and doctors.
Retail
Enhancing checkout efficiency at supermarkets.